Playing suspended bell music on the table
by Sueda and Jeff Luttrell
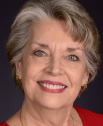
Sueda Luttrell is a native of Lufkin, Texas, and received Bachelor and Master of Music degrees in Organ Performance from Baylor University. She currently holds the position of Organist/Music Associate at Gambrell Street Baptist Church in Fort Worth. A clinician for Handbell Musicians of America, Greater Dallas Handbell Association, Church Music Institute, Baylor University’s Alleluia Conference, and Chorister’s Guild, she is also a published composer. She served Handbell Musicians of America as a board member in Areas 4 and 9 and presented the featured solo ringing concert at the guild’s 50th anniversary celebration in 2004. In addition, Sueda was the solo/ensemble representative for the 2010 Handbell and Handchime Notation Guide. Her ringing experience included membership in Golden Bells of Atlanta, Atlanta Bronze Ensemble, Concert Bells of Fort Worth, East Texas Handbell Ensemble, and Cast of Bronze.
Jeff Luttrell hails from Fort Worth, Texas, and received Bachelor and Master of Science degrees in Mechanical Engineering from Texas Tech University, followed by a Ph.D. in Mechanical Engineering from the University of Texas-Arlington. He currently holds the position of Environmental Control System lead engineer on the V-280 program at Bell Textron in Hurst, Texas.
His aerospace engineering career in environmental control and thermodynamics included several programs currently part of the US armed forces fleet: F-16, F-35, F-22, C-5M, and C-130J. In addition, he taught as an adjunct professor at TCU and the University of Texas-Arlington. His publications include two papers on aircraft icing and three on data center cooling.
Sueda and Jeff are the proud parents of two daughters and their husbands. The light of their lives is one gorgeous granddaughter.
Sueda: I am a career church musician, and organ is my primary instrument. After ringing in a bell choir as a teenager, I pursued that activity wherever I served as organist. My solo ringing journey began in 1995 and continued until my last solo concert in 2016. Increasing deterioration in my hands shifted my focus to remain active as an organist while leading occasional handbell workshops.
In 2021 I agreed to play two (malleted) bell tree solos as part of the Advent concert at a local church. The pieces chosen were “I Saw Three Ships” by Sandra Eithun and Linda Lamb (MHP2525) and an adaptation of a full-choir arrangement of “Savior of the Nations, Come” by Kath Wissinger (RELC201399LR and LC201399L). Kath composed a new introduction, incorporating bell tree with full bell choir, and added bell tree components throughout. While learning these works using four suspended bell trees, my mind wandered. My organist-self thought of a horizontal two “manual” (row) setup in keyboard order, including offset accidentals. The top row (C6-C7) would be a continuation of the lower (G4, C5-B5). I also envisioned “suspended en chamade” bells. En chamade organ pipes are powerful reeds mounted horizontally instead of vertically. Vertically-suspended trees are stunning, but this option intrigued me. I decided to reorient the trees from vertical to horizontal, combining the two-manual organ concept with the horizontal positioning of en chamade pipes. The bell tree-esque LV required all castings to be raised (suspended) above the tabletop. An elevated second row, as on an organ console, would facilitate malleting. I asked my personal engineer and husband, Jeff Luttrell, to help. After several revisions and Jeff’s unending patience, we share our results here. The entire G4 plus C5-C7 range fits on a 48” by 30” table with 4” foam.
Building the Framework
Jeff: In setting up the bells in two rows (keyboard order with offset accidentals), the larger bells are nearest the ringer (first row). The row of smaller bells is furthest from the ringer (second row), continuing chromatically from the first row, and rests on a pad to increase height. The pad is made with a thin sheet of 12” by 48” plywood and 1” foam pad, all covered with black cloth.
The handles on each row are held with a 1” steel pipe and two wooden 1” dowels. Each dowel has a cut taking off about ¼” to create a flat bottom to prevent rolling. Black felt is glued to the pipes and stapled to the dowels.
The pipe fits through the handles of the naturals and provides the counterweight to hold the lower part of the handles to the table. The first dowel of each row is threaded through the handles of the accidentals and acts to hold down the handles of the accidentals, elevate the handles of the naturals near the handguard, and raise their castings off the table. For the first row, the dowel through the handles of accidentals has a ¼” by ¼” groove to nest the handguards of the naturals. The second row has handles resting on the dowel.
The two dowels for the second row have added features. The dowel passing through the handles of the accidentals is topped with a layer of 3/8” by 1” weatherproofing foam tape, attached using the tape’s adhesive side. This layer of foam tape raises the bells slightly and improves tone. The other wooden dowel under the handles of the accidentals includes two layers of the same foam tape for additional height.
For ease of malleting, all accidentals are raised even higher than the lift afforded by the dowel and layers of foam tape. This is achieved with some ¾” rubber tips. Typically used over the ends of metal chair or table legs, these rubber tips are available in hardware stores. A hole drilled mid-way along the side of the rubber tips allows a plastic cable tie to pass through. The cable tie secures the rubber tips to the bell handles near the handguards. The accidentals rest their rubber tips directly atop the dowel for the first row and on top of the two layers of foam tape for the second row. This provides extra lift and angle for the accidentals.
For assembly, the handles of the second-row naturals are threaded on the metal pipes, while the handles of the accidentals are threaded on the appropriate dowel. The dowel with doubled foam tape is placed on the 12” by 48” by 1” pad; then, the second-row accidentals and dowel are lowered into place. Next, the pipe with the second-row naturals is lowered into position and the bells adjusted for spacing. The first-row bells are then arranged using the same approach.
Sueda: I do not recommend this method as a means to cover parts for missing ringers within a bell choir as the sound is far different from bells rung in-hand. Time must also be allowed for assembly/disassembly. However, it works very well for me as an alternate setup for major bell tree solos or other independent lines such as descants. Be fearless and pursue your own ideas!
Sueda playing “I Saw Three Ships” on suspended bell setup
More Photos
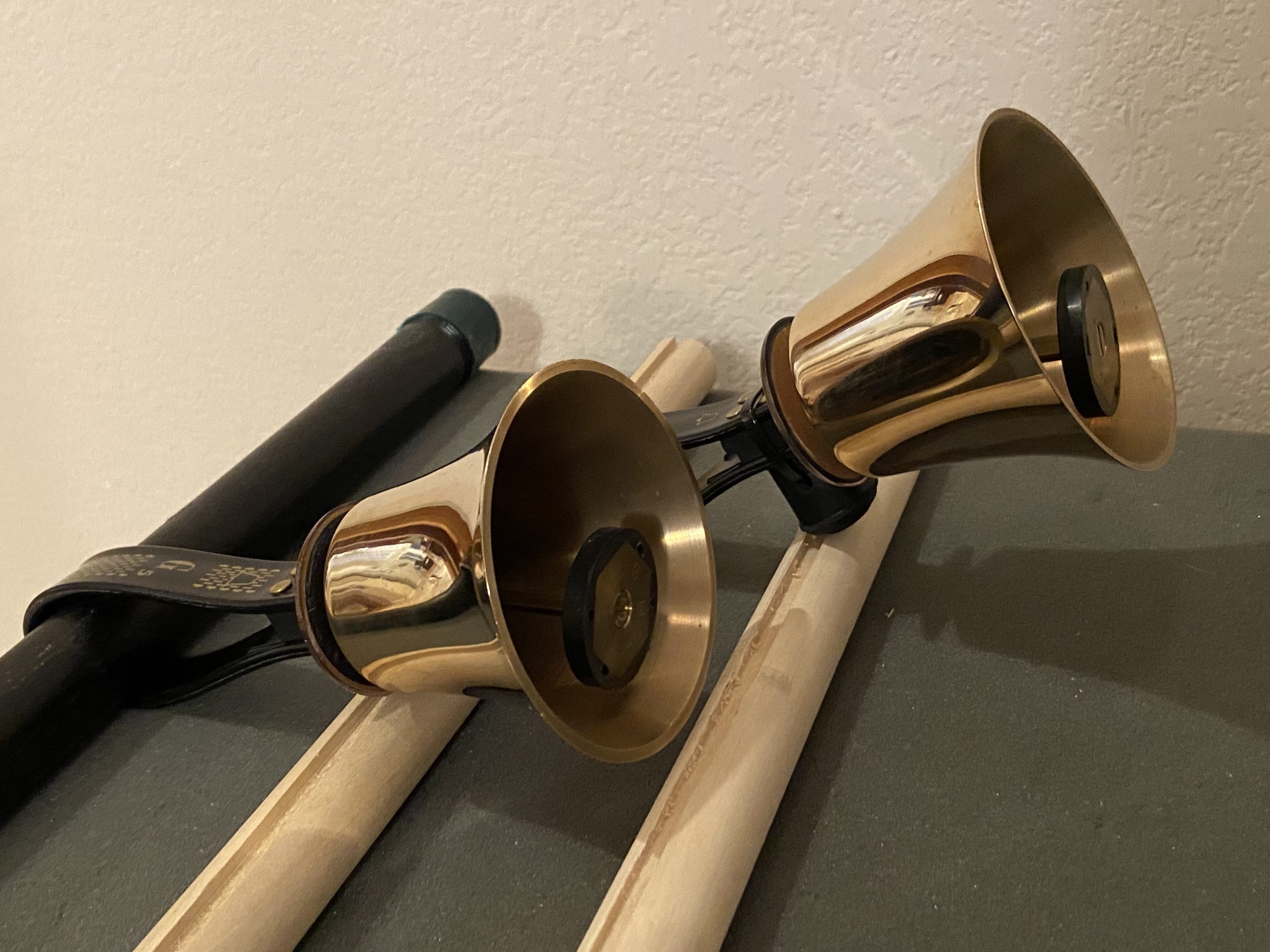
First Row
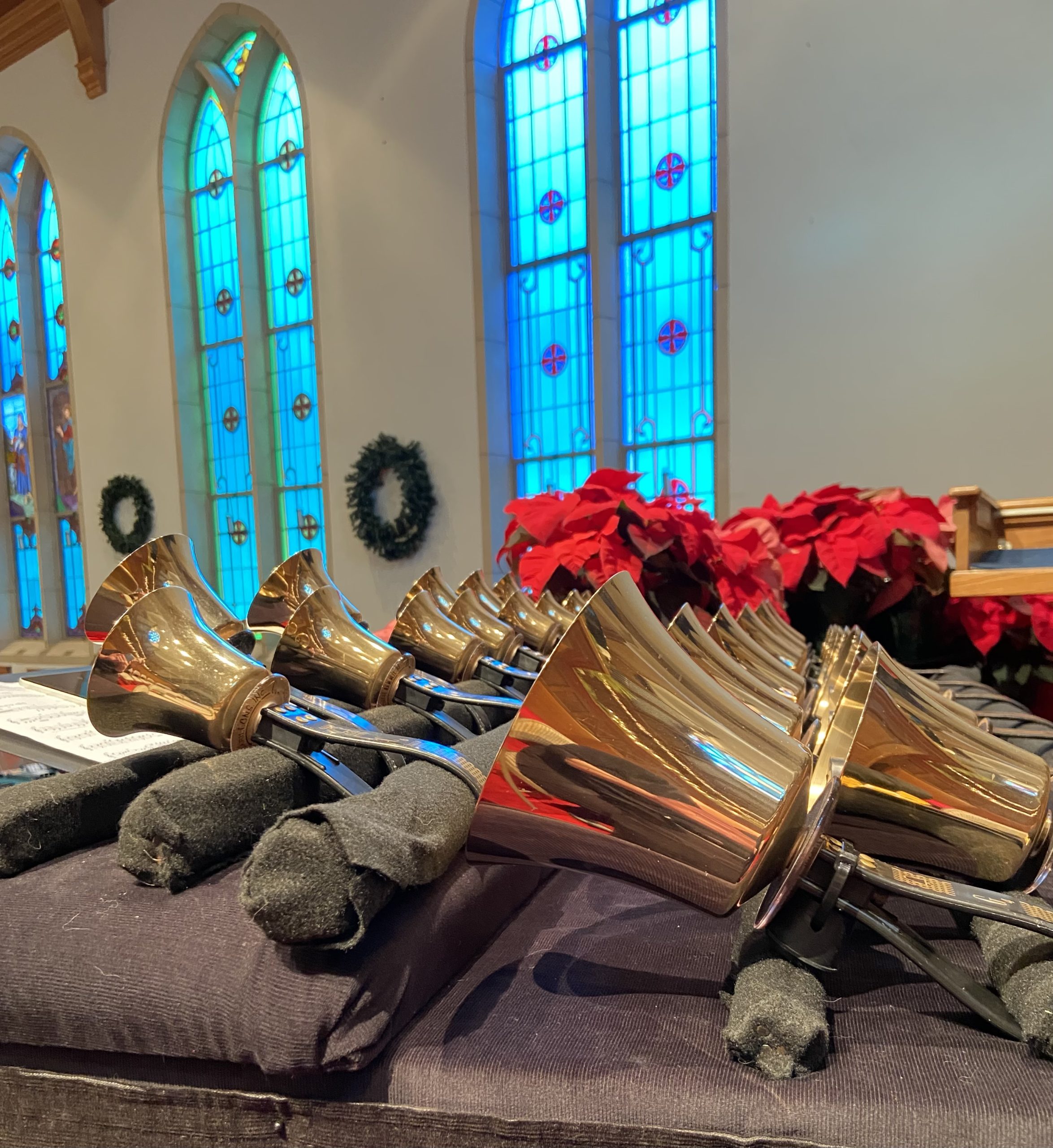
Full Dress
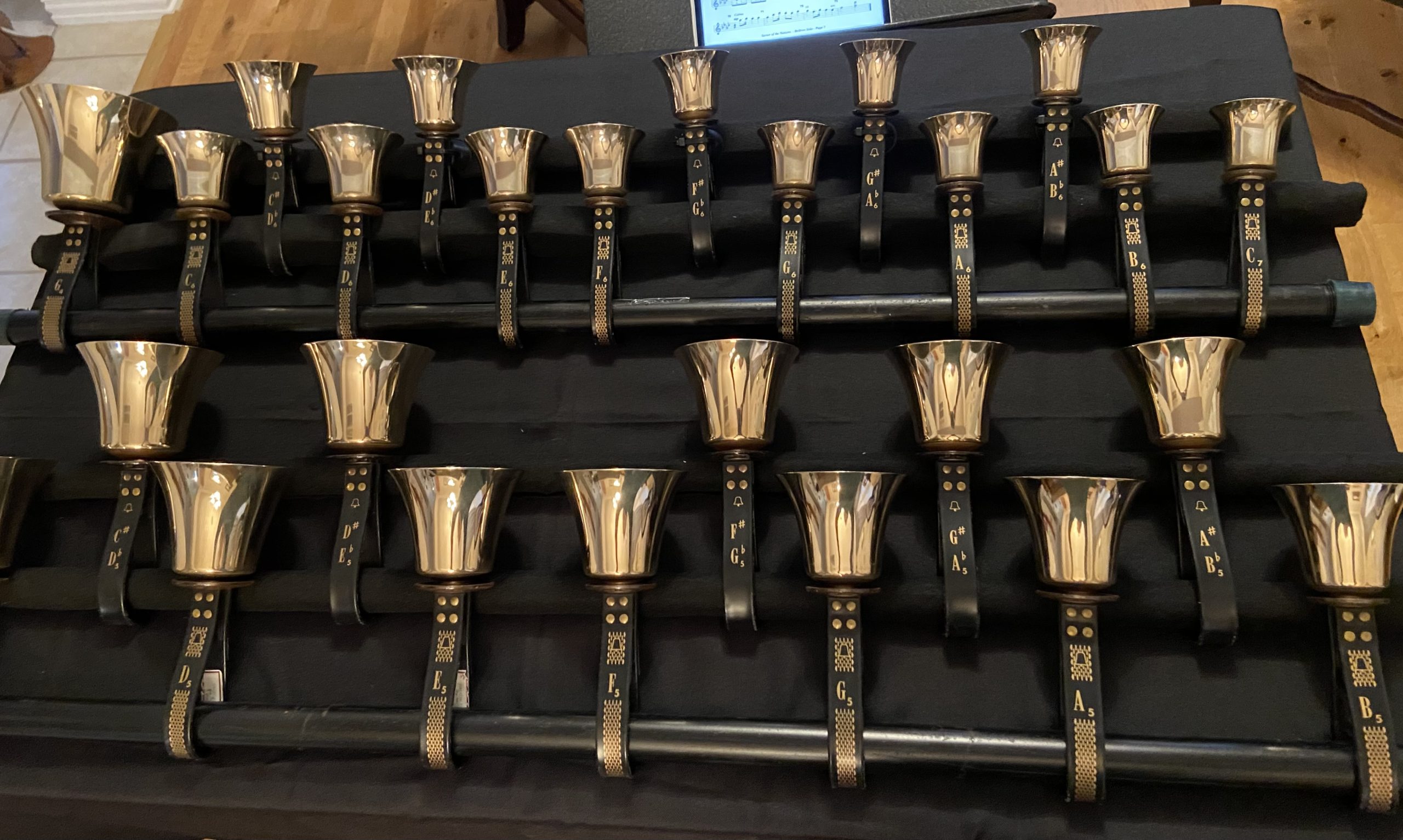
Early top view
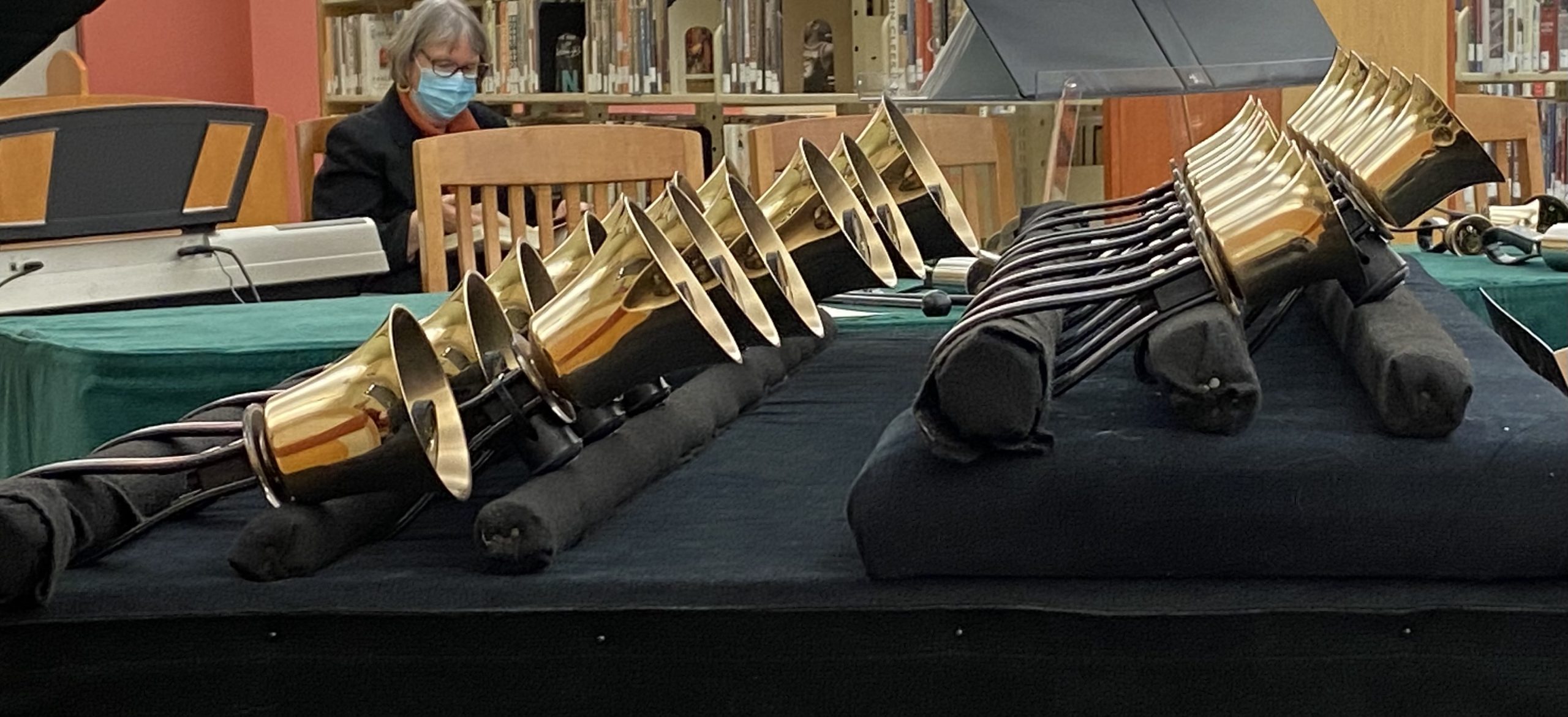
End view
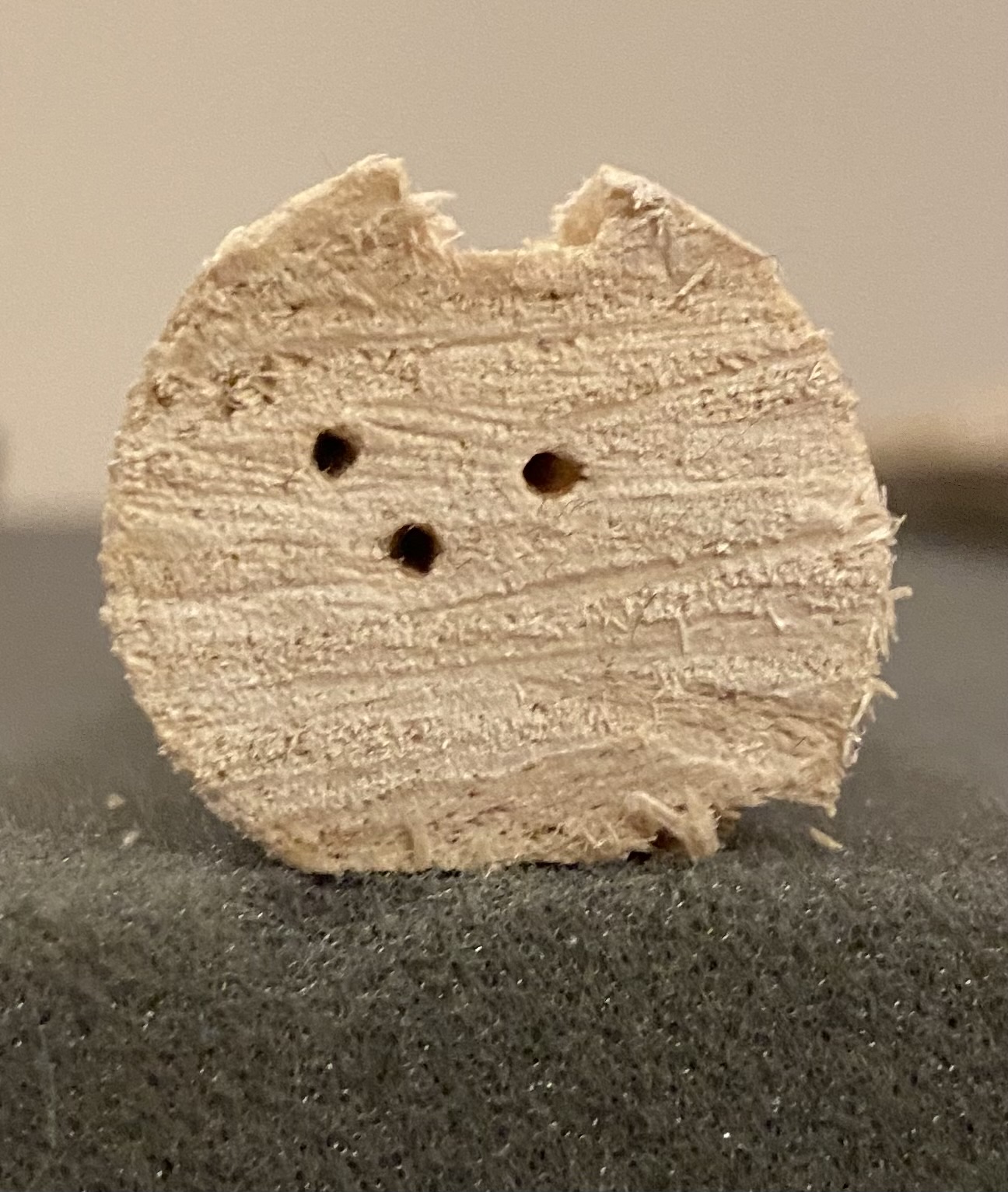
Grooved dowel
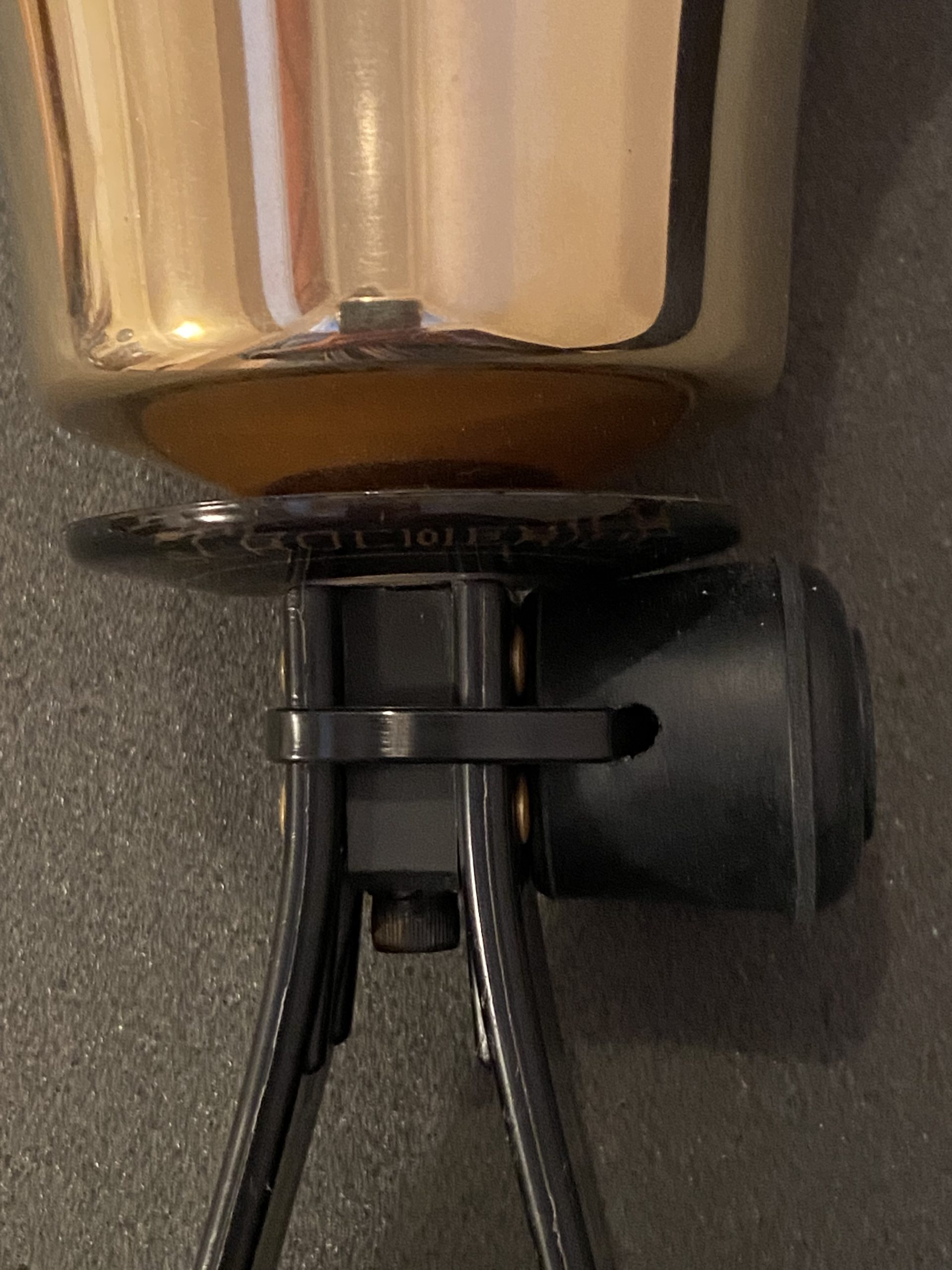
Cable tie
Sueda: I am a career church musician, and organ is my primary instrument. After ringing in a bell choir as a teenager, I pursued that activity wherever I served as organist. My solo ringing journey began in 1995 and continued until my last solo concert in 2016. Increasing deterioration in my hands shifted my focus to remain active as an organist while leading occasional handbell workshops.
In 2021 I agreed to play two (malleted) bell tree solos as part of the Advent concert at a local church. The pieces chosen were “I Saw Three Ships” by Sandra Eithun and Linda Lamb (MHP2525) and an adaptation of a full-choir arrangement of “Savior of the Nations, Come” by Kath Wissinger (RELC201399LR and LC201399L). Kath composed a new introduction, incorporating bell tree with full bell choir, and added bell tree components throughout. While learning these works using four suspended bell trees, my mind wandered. My organist-self thought of a horizontal two “manual” (row) setup in keyboard order, including offset accidentals. The top row (C6-C7) would be a continuation of the lower (G4, C5-B5). I also envisioned “suspended en chamade” bells. En chamade organ pipes are powerful reeds mounted horizontally instead of vertically. Vertically-suspended trees are stunning, but this option intrigued me. I decided to reorient the trees from vertical to horizontal, combining the two-manual organ concept with the horizontal positioning of en chamade pipes. The bell tree-esque LV required all castings to be raised (suspended) above the tabletop. An elevated second row, as on an organ console, would facilitate malleting. I asked my personal engineer and husband, Jeff Luttrell, to help. After several revisions and Jeff’s unending patience, we share our results here. The entire G4 plus C5-C7 range fits on a 48” by 30” table with 4” foam.
Building the Framework
Jeff: In setting up the bells in two rows (keyboard order with offset accidentals), the larger bells are nearest the ringer (first row). The row of smaller bells is furthest from the ringer (second row), continuing chromatically from the first row, and rests on a pad to increase height. The pad is made with a thin sheet of 12” by 48” plywood and 1” foam pad, all covered with black cloth.
The handles on each row are held with a 1” steel pipe and two wooden 1” dowels. Each dowel has a cut taking off about ¼” to create a flat bottom to prevent rolling. Black felt is glued to the pipes and stapled to the dowels.
The pipe fits through the handles of the naturals and provides the counterweight to hold the lower part of the handles to the table. The first dowel of each row is threaded through the handles of the accidentals and acts to hold down the handles of the accidentals, elevate the handles of the naturals near the handguard, and raise their castings off the table. For the first row, the dowel through the handles of accidentals has a ¼” by ¼” groove to nest the handguards of the naturals. The second row has handles resting on the dowel.
The two dowels for the second row have added features. The dowel passing through the handles of the accidentals is topped with a layer of 3/8” by 1” weatherproofing foam tape, attached using the tape’s adhesive side. This layer of foam tape raises the bells slightly and improves tone. The other wooden dowel under the handles of the accidentals includes two layers of the same foam tape for additional height.
For ease of malleting, all accidentals are raised even higher than the lift afforded by the dowel and layers of foam tape. This is achieved with some ¾” rubber tips. Typically used over the ends of metal chair or table legs, these rubber tips are available in hardware stores. A hole drilled mid-way along the side of the rubber tips allows a plastic cable tie to pass through. The cable tie secures the rubber tips to the bell handles near the handguards. The accidentals rest their rubber tips directly atop the dowel for the first row and on top of the two layers of foam tape for the second row. This provides extra lift and angle for the accidentals.
For assembly, the handles of the second-row naturals are threaded on the metal pipes, while the handles of the accidentals are threaded on the appropriate dowel. The dowel with doubled foam tape is placed on the 12” by 48” by 1” pad; then, the second-row accidentals and dowel are lowered into place. Next, the pipe with the second-row naturals is lowered into position and the bells adjusted for spacing. The first-row bells are then arranged using the same approach.
Sueda: I do not recommend this method as a means to cover parts for missing ringers within a bell choir as the sound is far different from bells rung in-hand. Time must also be allowed for assembly/disassembly. However, it works very well for me as an alternate setup for major bell tree solos or other independent lines such as descants. Be fearless and pursue your own ideas!
Sueda playing “I Saw Three Ships” on suspended bell setup
More Photos
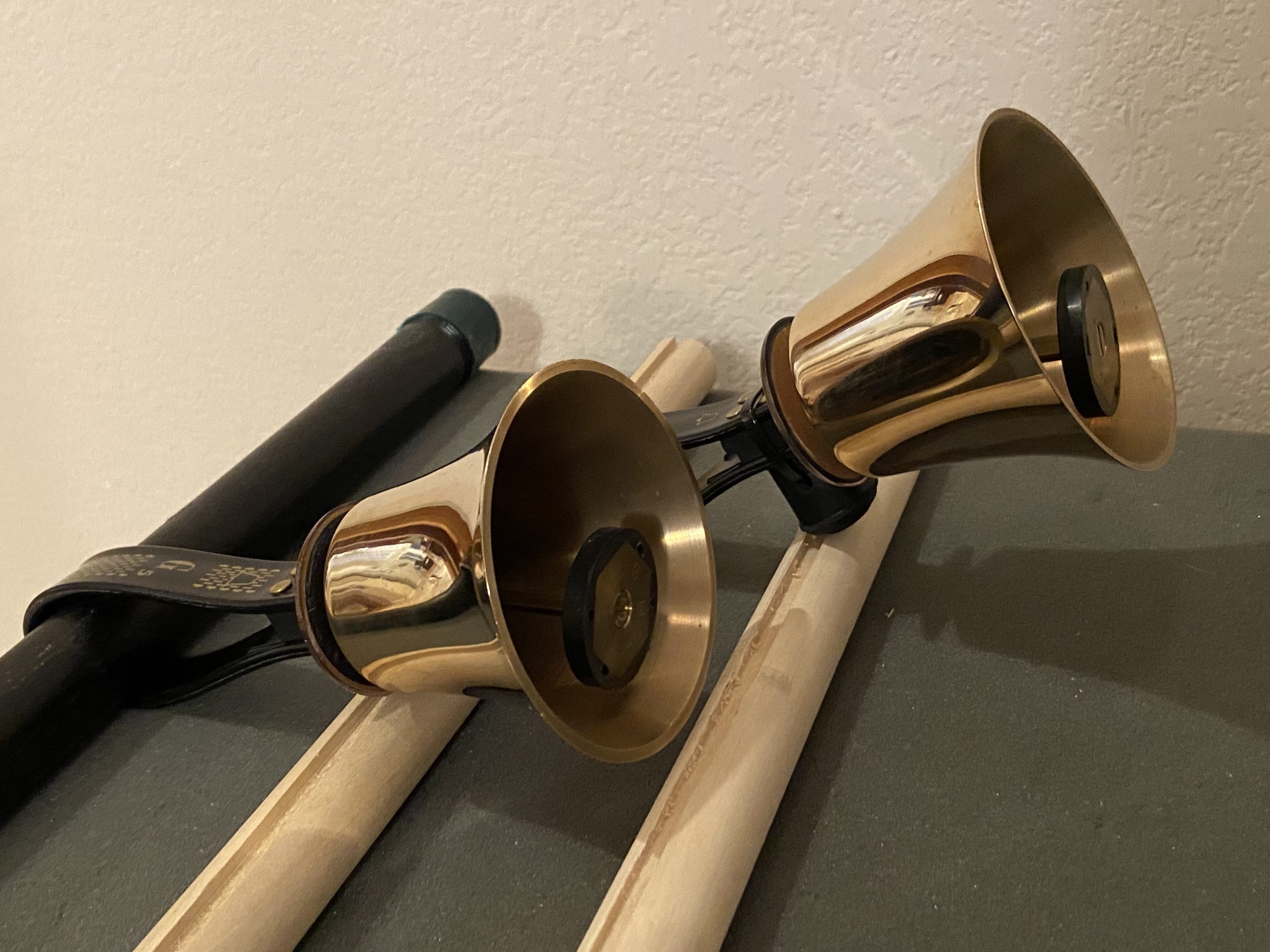
First Row
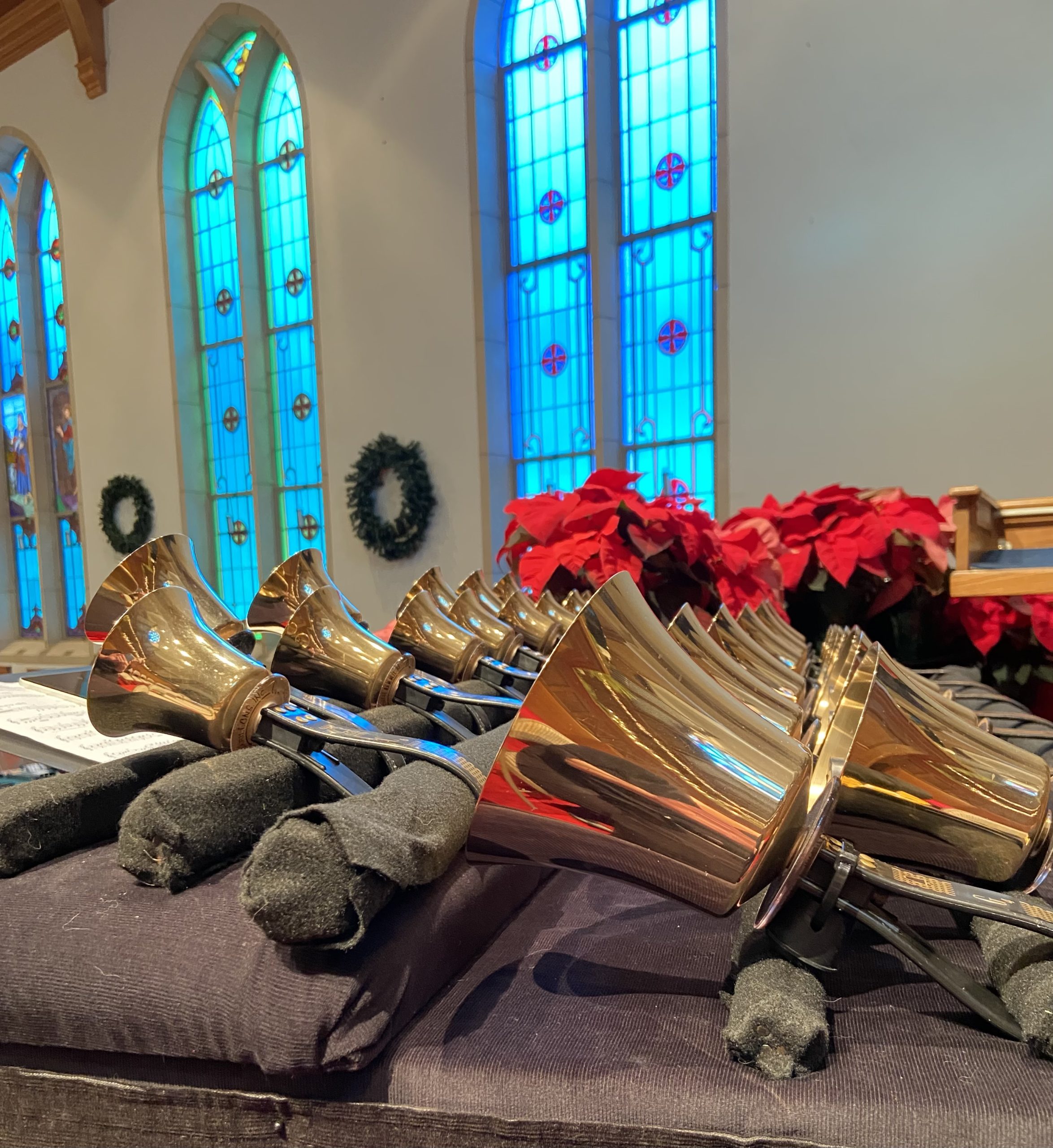
Full Dress
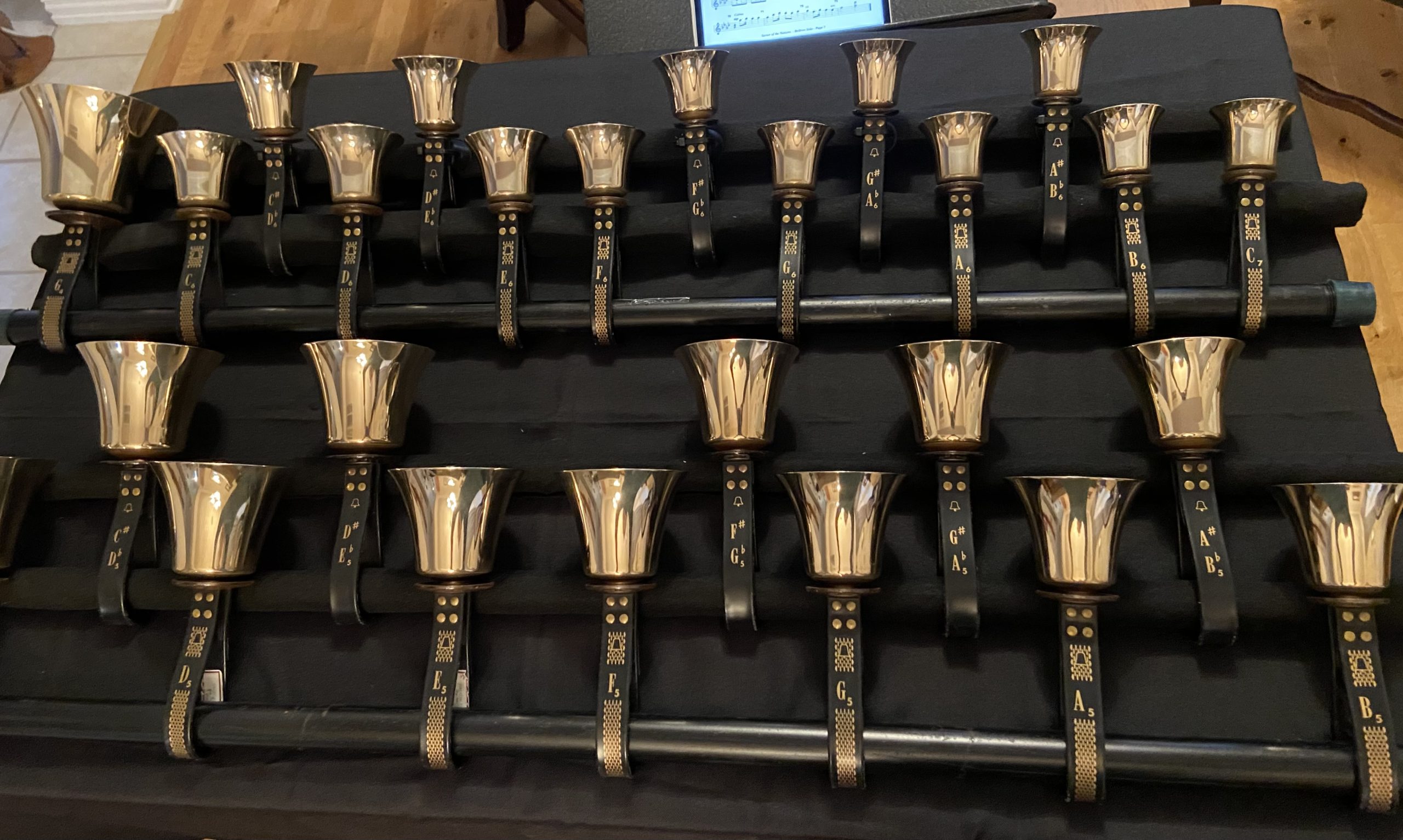
Early top view
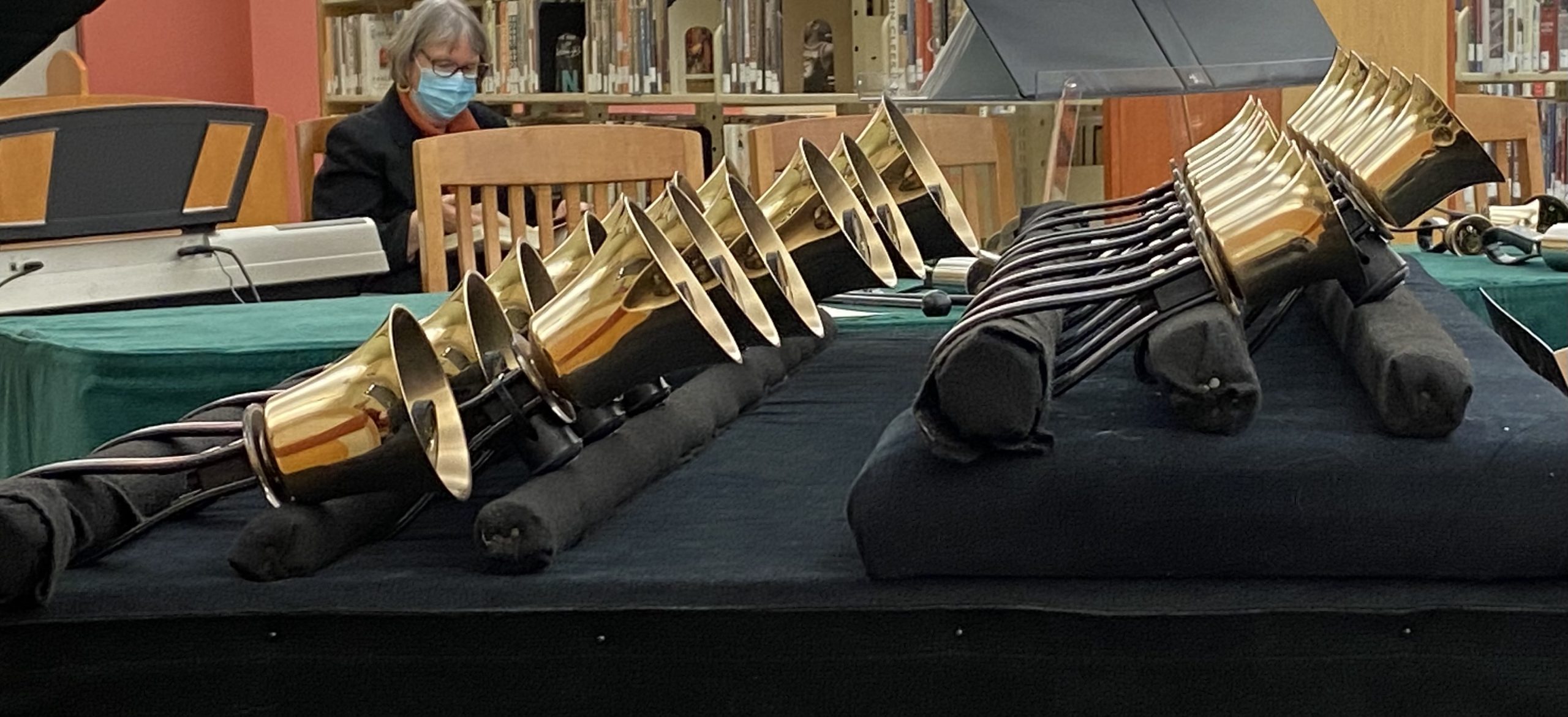
End view
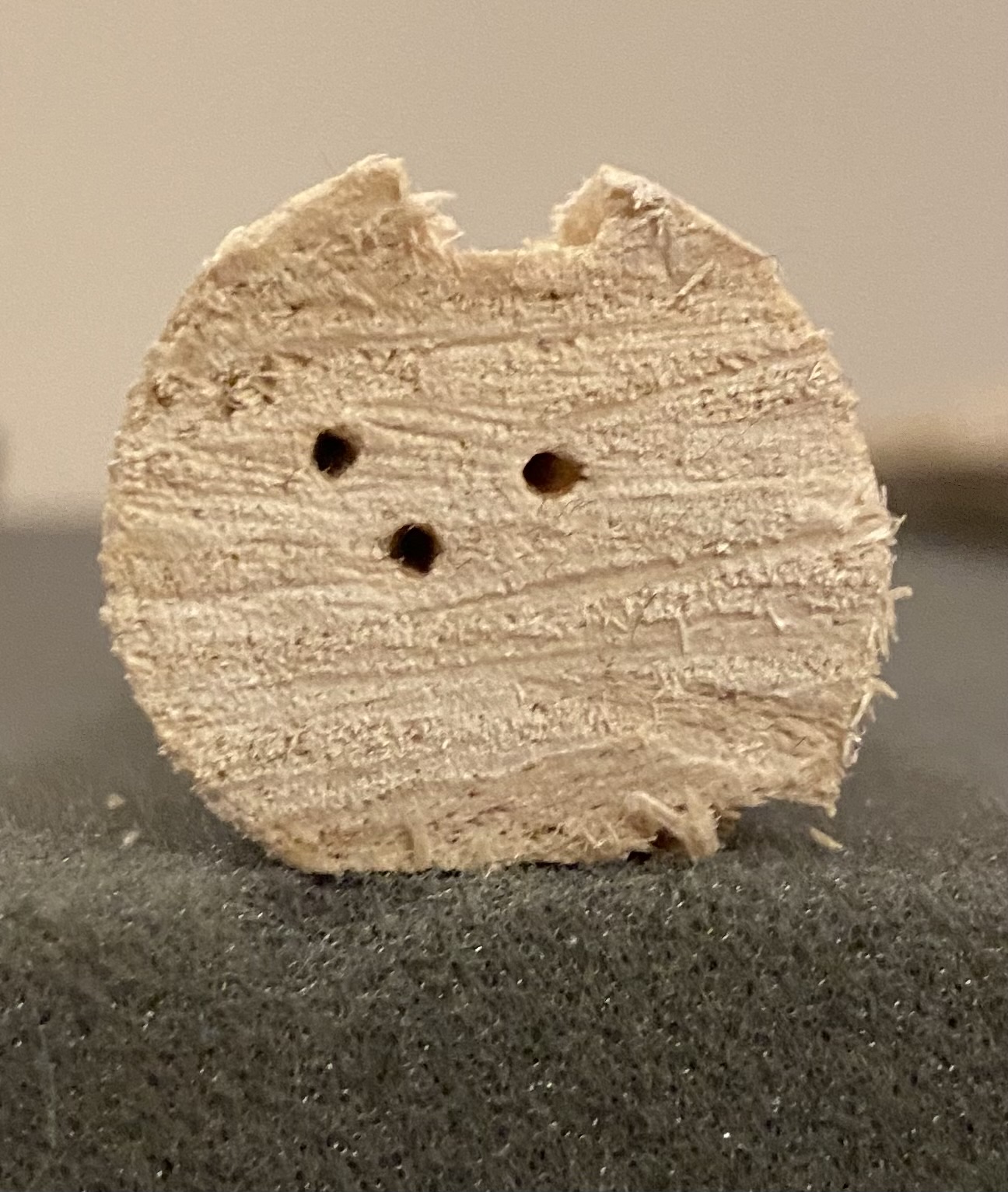
Grooved dowel
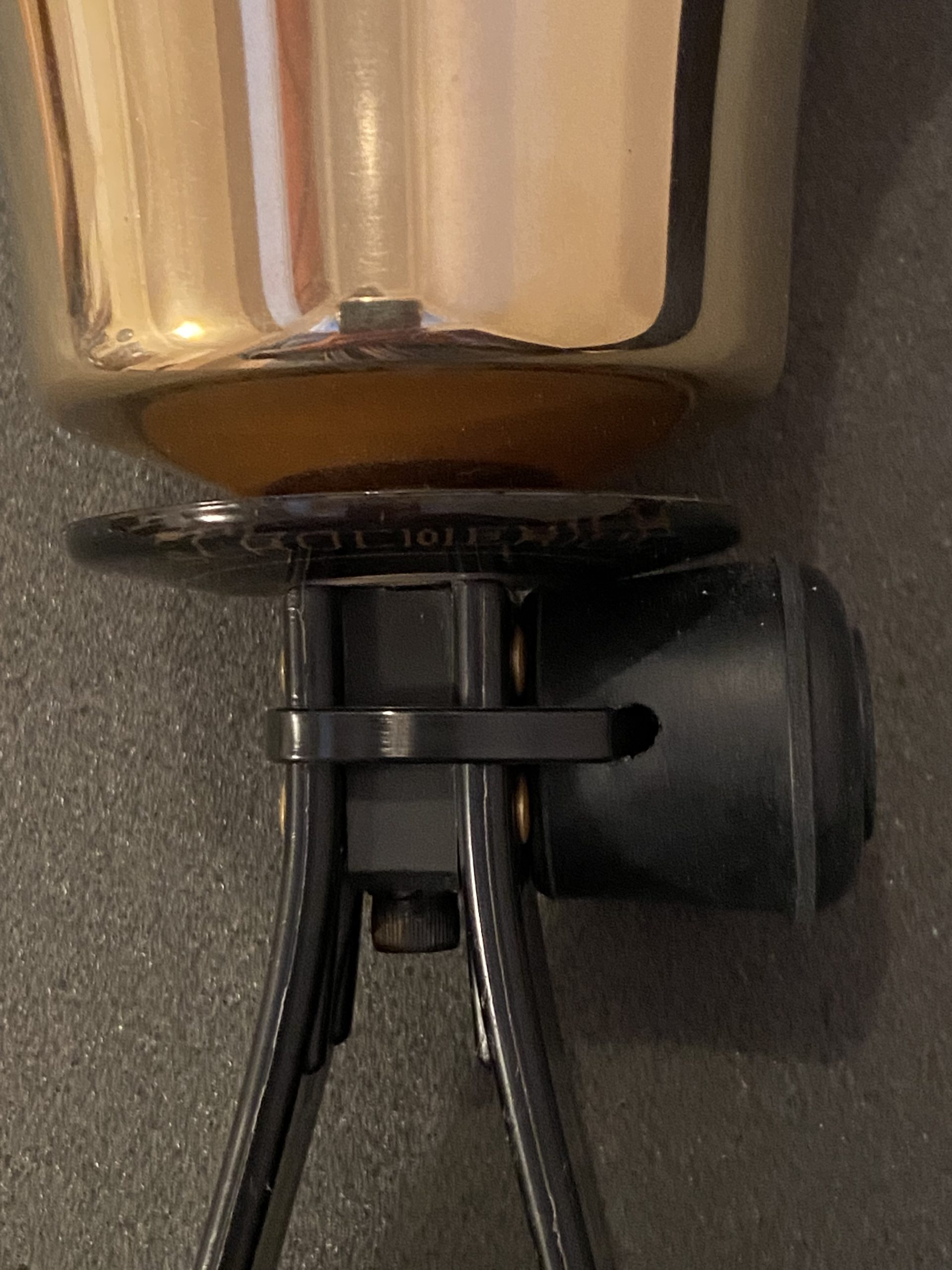
Cable tie
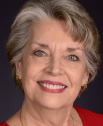
Sueda Luttrell is a native of Lufkin, Texas, and received Bachelor and Master of Music degrees in Organ Performance from Baylor University. She currently holds the position of Organist/Music Associate at Gambrell Street Baptist Church in Fort Worth. A clinician for Handbell Musicians of America, Greater Dallas Handbell Association, Church Music Institute, Baylor University’s Alleluia Conference, and Chorister’s Guild, she is also a published composer. She served Handbell Musicians of America as a board member in Areas 4 and 9 and presented the featured solo ringing concert at the guild’s 50th anniversary celebration in 2004. In addition, Sueda was the solo/ensemble representative for the 2010 Handbell and Handchime Notation Guide. Her ringing experience included membership in Golden Bells of Atlanta, Atlanta Bronze Ensemble, Concert Bells of Fort Worth, East Texas Handbell Ensemble, and Cast of Bronze.
Jeff Luttrell hails from Fort Worth, Texas, and received Bachelor and Master of Science degrees in Mechanical Engineering from Texas Tech University, followed by a Ph.D. in Mechanical Engineering from the University of Texas-Arlington. He currently holds the position of Environmental Control System lead engineer on the V-280 program at Bell Textron in Hurst, Texas.
His aerospace engineering career in environmental control and thermodynamics included several programs currently part of the US armed forces fleet: F-16, F-35, F-22, C-5M, and C-130J. In addition, he taught as an adjunct professor at TCU and the University of Texas-Arlington. His publications include two papers on aircraft icing and three on data center cooling.
Sueda and Jeff are the proud parents of two daughters and their husbands. The light of their lives is one gorgeous granddaughter.